Improving problem identification and resolution speed through dual disciplines.
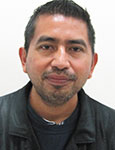
Teams at multiple SigmaTron International facilities have been trained in Lean Six Sigma philosophy. However, some companies work from a pure Lean manufacturing philosophy without Six Sigma tools. This month, we look at the benefits of integrating these disciplines.
Any company embracing Lean manufacturing philosophy generally focus on eliminating the seven wastes:
- Waste of overproducing (no immediate need for product being produced)
- Waste of waiting (idle time between operations)
- Waste of transport (product moving more than necessary)
- Waste of processing (doing more than what has been agreed upon)
- Waste of inventory (excess above what was required)
- Waste of motion (any motion not necessary outside of production)
- Waste of defects (producing defects requiring rework).
Done holistically in a normal materials-availability environment, this improves throughput while reducing inefficiency and the unplanned variations that lead to defects. Adding Six Sigma to the equation gives employees the tools and training to fine-tune this system. Simply put:
- Lean = capable (oriented to wastes)
- Six Sigma = effective (oriented to defects reduction)
- Lean Six Sigma = capable and effective.
In the electronics manufacturing services (EMS) industry, the bigger question is: What are the benefits of Lean Six Sigma to customers? EMS customers consider quality a given in the outsourcing relationship. In short, they often look at the result, rather than the disciplines used to achieve the result. That said, Lean Six Sigma provides specific benefits in the current environment. These include:
- Force-multiplying employees focused on continuous improvement. When employees have the tools and training to identify waste and correct the issue, programs run smoother.
- Smoother new product introduction (NPI). NPI has a large learning curve and resource demands for both customer and contract manufacturer teams. When the contract manufacturer team is working from a Lean Six Sigma perspective, issues tend to be better documented, and resolutions are identified and validated more quickly, thanks to core tools such as the Define, Measure, Analyze, Improve, Control (DMAIC) process. This can lower time demands on customers during this period.
- Faster issue identification/resolution. The current business environment has created many external drivers of defects, from materials quality issues due to supply/demand imbalances, to the production challenges created by unexpectedly steep spikes in product demand. Lean Six Sigma culture drives a focus on metrics that helps identify and correct these issues as they begin.
- Improved cycle time. Another dynamic in the current environment is that materials-availability delays impact production schedules on a regular basis. A Lean Six Sigma environment has faster line changeovers and more focus on eliminating the variation that impacts throughput, allowing a faster response to unplanned schedule changes.
There are also benefits at the employee level that improve productivity and retention:
- Greater opportunities for recognition of meaningful accomplishments. Because continuous improvement activities are team-based and well documented, the value of these activities is evident to a larger number of contributing employees and higher levels of the organization.
- Job enlargement/enrichment. Production activities are repetitive by design and that can create job dissatisfaction. Employees in a Lean Six Sigma environment receive the training and tools to increase skills and expertise over time, plus add the variation of kaizen events to their work environment.
- Improved quality focus. The more employees understand the “why” behind work instructions and process control metrics, the harder they are likely to work to ensure the process stays within control limits. A Lean Six Sigma culture helps distribute this knowledge across a wider employee base and create a bottom-up focus on driving positive results.
The bottom line is that a Lean Six Sigma approach helps create a workforce that better understands the results of their actions, is more able to identify emerging quality issues, and can more rapidly evaluate and implement viable solutions to the problems they identify. While Lean manufacturing alone can address much of this in terms of product and process design, the addition of Six Sigma tools and training helps improve problem identification and resolution speed by educating a larger pool of employees in these skill sets. This “working smarter” approach creates a more efficient, productive organization better able to adapt to the challenges facing manufacturers today. •
Filemon Sagrero is continuous improvement engineer and a Six Sigma Black Belt at SigmaTron International’s facility in Tijuana, Mexico; filemon.sagrero@sigmatronintl.com.